Digital Twin
Explore intuitive vibration diagnosis
Digital Twin
Explore intuitive vibration diagnosis
Intro
It’s all about Data-Driven Decision Making
The industry faces challenges in optimizing production processes and achieving climate-neutrality while managing costs. Digital Twin technologies offer solutions to these challenges. The Digital Twin is a tool for enhancing availability and productivity, reducing maintenance and energy/environmental costs, and enabling informed decision-making based on operational data.
But what is the Digital Twin? For us, it’s a unique digital representation mirroring the physical object. Integrating all relevant data into a dynamic multi-domain model, it evolves throughout the plant lifecycle to remain an up-to-date counterpart. The combination of operational experience and our expertise in process engineering, instrumentation and control creates a synergy that unlocks amazing opportunities!
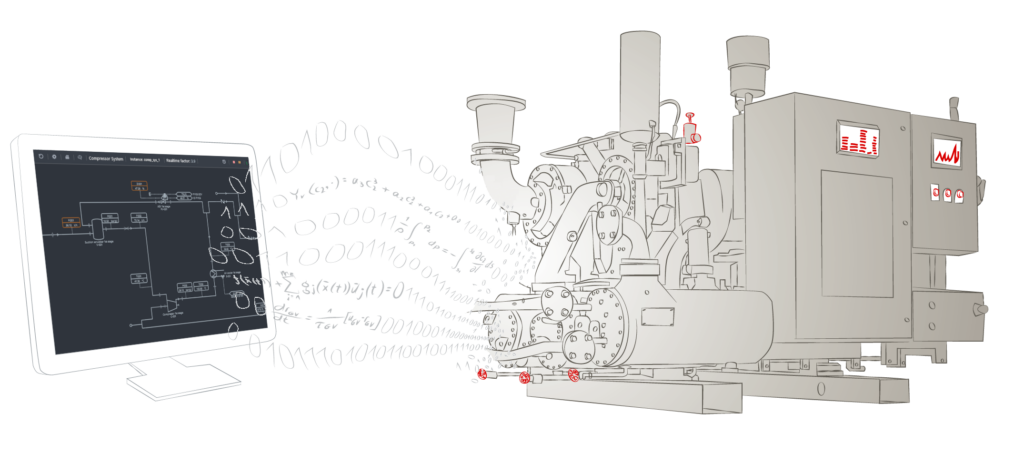

Services
Following Plant’s Lifecycle
The Digital Twin supports decision-making throughout the entire plant lifecycle, from planning to modernization. It generates a highly accurate, dynamic process model using provided design and process data. Our simulation environment, equipped with powerful optimization algorithms, drives the evolution of the Digital Twin throughout its lifecycle. By merging design and field data, it provides a holistic view of the plant, offering valuable insights into its operation.

Use Cases
Explore amazing Opportunities
Integration
?????
Hardware Integration
Software Integration
Features
??????
Raw data – Save raw data snapshots using time- and event-based triggers including pre- and post-event data
Performing – Intelligent data management scheme for maximum data transfer performance and analysis speed
Analysis – Perform ad-hoc vibration analysis on every snapshot like FFT, Orbit, ISO10816
Purposeful – The Flight Recorder only records relevant machine events, ensuring that no unnecessary data is stored
Multi-Purpose – 6 galvanically isolated multi-purpose analog inputs for proximitors, keyphasors, transmitter & rack Buffered Out connectors as well as velocity, acceleration, speed & dynamic pressure sensors
Multi-Power – Each channel can be configured as 2-wire (IEPE 6mA), 3-wire (+24VDC / -24VDC supply) our without power supply.
Multi-Range – Measure sensor data in unipolar range 0 .. ±24V or bipolar range ±24V.
High Quality – 24bit time synchronous sampling @ 100kHz
Small Size – IP20 casing with DIN rail mounting, 45 x 120 x 120mm
Connected – 2x GbE RJ45
Industrial Range – From -20 to +65°C operating temperature @ 10 .. 90% humidity
Optimized – The Gateway ensures high data throughput, storing full-resolution data for around 2 years (typical use), with automatic data reduction at max database capacity.
Trusted – Our METIS software relies on an long-term supported industrial Linux OS from Siemens.
Small Size – Big performance, small footprint. Instead of using big server racks we are using robust IPCs: Small (85 x 85 x 41mm) or Large (191 x 100 x 60mm).
Small Gateway – Quad Atom E3940, 4 GB RAM, 64/128 GB SSD, 2x GbE RJ45, 1x DisplayPort, DIN rail mount
Large Gateway – Quad Celeron N2930, 8 GB RAM, 128/240/480 GB SSD, 2x GbE RJ45, 1x DisplayPort, DIN rail mount
Turbo compressor shaft vibration
Gearbox vibration
Reciprocating compressor vibration
Pump and fan vibration
Housing & bearing vibration
Machine-to-Machine – OPC UA, Modbus TCP, GE Historian Client
Manual Export – JSON, XLS/CSV, NI TDMS, Matlab® MAT
Direct Access – REST API
Expandable – Additional M2M and Export Connectors can be provided on request
Contact
Dr. Rico Schulze
Rico.Schulze@avicomp.com
+49 341 21787 1791
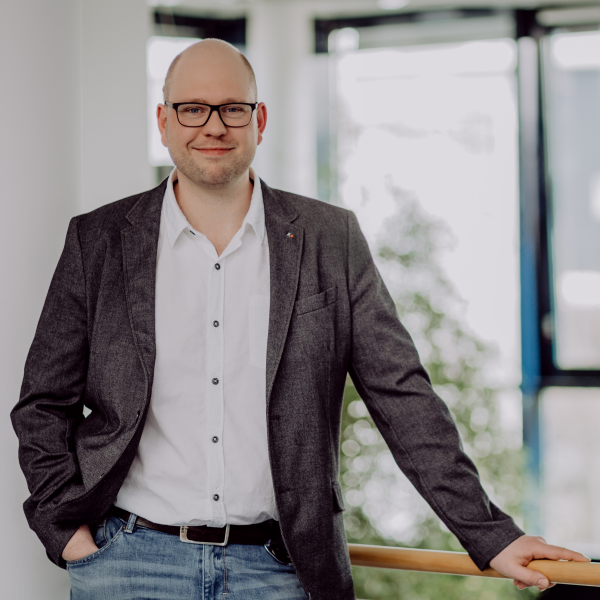
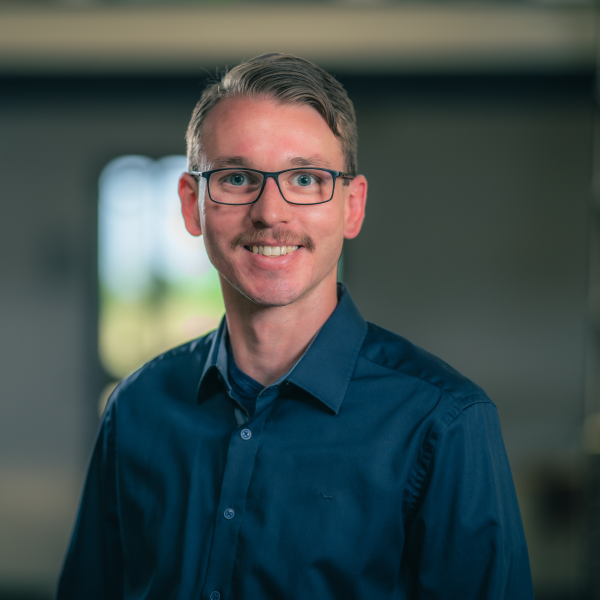
Kevin Schleifer
Kevin.Schleifer@avicomp.com
+49 341 21787 1784